德百世(DeVilbiss)制氧机24小时服务热线全国售后服务电话受理客服中心400-021-6681
德百世(DeVilbiss)制氧机24小时服务热线全国售后服务电话受理客服中心400-021-6681德百世(DeVilbiss)制氧机24小时服务热线全国售后服务电话受理客服中心400-021-6681
压缩机异响:故障原因与解决方法400-021-6681
压缩机异响,是指 “设备核心气体压缩部件在运转时,产生超出正常范围的声音”,表现为 “原本平稳的运行声中混入金属摩擦音”“周期性的敲击声(频率与转速一致)”“高频啸叫声(随压力升高增强)”“不规则的咔哒声(偶发或持续)”。正常运行的压缩机声音应 “连续稳定”(声压级 55-65dB),频谱集中在 200-500Hz,而异响的声压级通常超过 70dB,且包含明显的高频成分(1000Hz 以上)。这类故障的核心是 “机械部件异常接触”“气流扰动加剧” 或 “振动传递放大”,若长期忽视,可能导致部件磨损加速(如轴承间隙从 0.01mm 增至 0.1mm)、效率下降(能耗增加 15%-30%),甚至突然停机。本文将从 “机械摩擦 - 气流扰动 - 振动传递” 三个层面,拆解异响产生的机制,提供从润滑调整到部件更换的完整解决方案,不依赖具体设备类型即可通用排查。
一、机械部件异常接触:金属摩擦引发的 “结构性异响”
压缩机的机械结构(如活塞与缸体、轴承与轴颈)需保持 “间隙配合”(正常 0.01-0.05mm),若因 “磨损超标”(间隙增至 0.1mm 以上)、“装配错位”(同轴度偏差>0.05mm)导致 “硬接触”,会产生 “金属摩擦音”“敲击音”,这类异响占比约 60%,且随运行时间延长逐渐加剧。
1. 运动部件的磨损与配合间隙超标
往复式压缩机的 “活塞裙部与缸体壁间隙过大”(从 0.03mm 增至 0.1mm),会导致 “活塞在缸内晃动”,形成 “径向敲击”(每转一圈撞击一次缸壁),发出 “规律性的咚咚声”,且随压力升高(活塞受力增大)异响加剧。旋转式压缩机的 “转子与定子间隙不均”(局部间隙 0.02mm,局部 0.1mm),会因 “单侧摩擦” 产生 “持续的沙沙声”,拆解后可见摩擦面有明显划痕(深度>0.01mm)。
滚动轴承的 “滚珠与滚道磨损”(表面粗糙度从 Ra0.4μm 升至 Ra1.6μm),会导致 “运转时产生周期性振动”,发出 “高频的嗡嗡声”(频率与转速成正比)。滑动轴承的 “轴颈磨损”(圆度误差>0.02mm)会使 “油膜无法稳定形成”,出现 “干摩擦瞬间”,表现为 “间歇性的尖锐摩擦音”,伴随轴承温度升高(超过环境温度 40℃)。
解决方法:
- 活塞 / 转子与缸体间隙超标的需 “更换磨损部件”(如活塞环、转子),确保间隙恢复至 0.02-0.05mm;装配时用 “百分表校准同轴度”(偏差<0.03mm),往复式压缩机需检查 “活塞销与连杆衬套间隙”(控制在 0.01-0.03mm)。
- 轴承磨损的需 “整体更换同型号轴承”(选用高精度等级 P5 级以上),轴颈磨损的需 “镀铬修复或更换主轴”(确保圆度误差<0.01mm),更换后测试 “空转异响”(应无明显金属摩擦音)。
2. 紧固部件的松动与脱落
固定缸体、端盖的 “螺栓松动”(预紧力从 20N?m 降至 5N?m)会导致 “部件间产生相对位移”,在压力波动时发出 “金属撞击声”(如缸体与底座的撞击),且随振动加剧松动进一步恶化。连杆螺栓若 “松动”(扭矩不足),会使 “连杆大头与曲轴间隙增大”,产生 “周期性的敲击声”(频率与曲轴转速一致)。
压缩机内部若混入 “金属碎屑”(如加工残留的铁屑)或 “硬质颗粒”(如过滤器脱落的纤维),会被 “卷入运动部件间隙”,导致 “瞬间卡滞”,发出 “尖锐的咔嚓声”,可能伴随运转卡顿(转速波动>100rpm)。长期卡滞会造成 “部件二次磨损”(如活塞被划伤),使异响从间歇性变为持续性。
解决方法:
- 松动螺栓需 “按规定扭矩重新紧固”(参考设备手册,如缸体螺栓 25N?m),重要部位加装 “防松垫圈”(如弹簧垫圈、止动垫片);连杆螺栓需使用 “扭矩扳手精确控制”,确保两端受力均匀。
- 内部有异物的需 “拆解压缩机彻底清洁”(用无水乙醇冲洗内部腔体),检查并去除所有碎屑,装配前用 “压缩空气吹扫”(确保无残留),必要时更换过滤器(防止异物再次进入)。
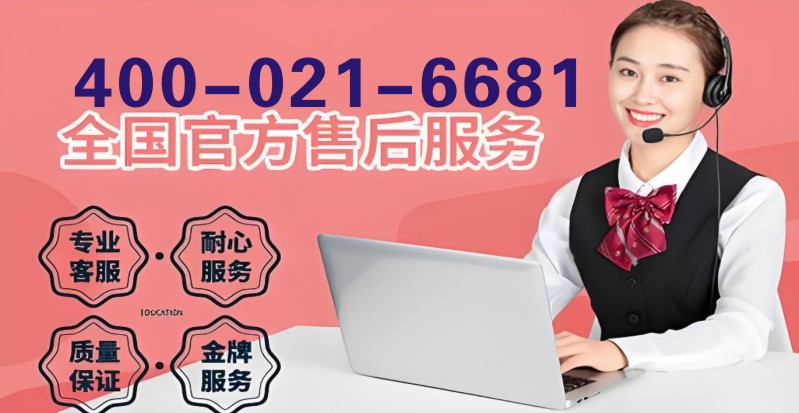
二、气流扰动与气阀异常:气体流动引发的 “气动性异响”
压缩机在 “吸气 - 压缩 - 排气” 循环中,若 “气流速度突变”(如气阀开启瞬间流速从 10m/s 增至 30m/s)、“压力脉动”(排气压力波动>5%),会产生 “气动噪声”,表现为 “啸叫声”“气流冲击声”,这类异响与机械摩擦音的区别是 “关闭电源后异响立即消失”(无机械惯性异响)。
1. 气阀组件的异常与气流扰动
吸气阀 / 排气阀的 “弹簧刚度异常”(如原 1N/mm 变为 0.5N/mm)会导致 “阀门开启过度”,气流高速冲击阀座产生 “涡流噪声”,发出 “持续的啸叫声”(频率 2000-5000Hz)。气阀 “关闭滞后”(延迟 0.01 秒)会使 “气体回流”(排气时部分气体倒流回压缩腔),形成 “压力脉动”,表现为 “低频的咚咚声”(与排气频率一致)。
气阀的 “阀片与阀座密封不良”(间隙>0.01mm)会导致 “气体持续泄漏”,泄漏气流在间隙处形成 “湍流”,发出 “嘶嘶声”,且随压力升高(泄漏量增大)异响增强。阀片若 “变形”(平面度误差>0.02mm)会使 “密封面接触不均”,出现 “局部高速气流”,表现为 “间歇性的气流冲击声”。
解决方法:
- 气阀弹簧刚度异常的需 “更换同规格弹簧”(确保弹力偏差<5%),调整阀门开启高度(控制在 0.5-1mm),减少气流冲击;关闭滞后的需 “检查阀片重量”(过重需更换轻质阀片),确保关闭响应时间<0.005 秒。
- 密封面泄漏的需 “研磨阀片与阀座”(确保平面度误差<0.01mm),变形严重的需更换阀片;装配时确保 “阀片运动无卡滞”(用手推动应灵活),必要时更换整组气阀组件。
2. 气流通道的结构与压力脉动
进气口若 “管径突变”(如从 φ10mm 骤变为 φ6mm)会导致 “气流速度骤升”(从 15m/s 增至 40m/s),形成 “湍流噪声”,发出 “高频的呼啸声”。排气管道若 “长度与直径不匹配”(如长径比>30)会引发 “管道共振”,使 “压力脉动放大”,表现为 “周期性的轰鸣声”(频率与管道固有频率一致)。
进气过滤器 “部分堵塞”(阻力从 50Pa 增至 300Pa)会使 “进气量不稳定”,导致 “压缩腔进气不足”,形成 “负压脉动”,发出 “抽吸式的呜呜声”。堵塞物若 “松动”(如纤维碎屑)会随气流振动,产生 “间歇性的哨笛声”,随过滤器清洁(阻力下降)异响减轻。
解决方法:
- 通道管径突变的需 “增加过渡段”(如锥形过渡,长度≥5 倍管径差),减少湍流;管道共振的需 “加装消声器”(如抗性消声器,降低特定频率噪声)或调整管道长度(避开共振频率)。
- 过滤器堵塞的需 “清洁或更换过滤器”(确保阻力<100Pa),避免使用孔径不均的过滤介质;进气口加装 “气流稳定器”(如多孔板),减少气流脉动。
三、振动传递与安装异常:结构共振放大的 “继发性异响”
压缩机的 “机械振动”(正常振幅<0.01mm)若通过 “安装结构”(如底座、支架)传递至设备外壳,并引发 “共振”(外壳固有频率与振动频率一致),会使异响放大(声压级提升 10-20dB),表现为 “设备整体发出轰鸣声”,这类异响的特征是 “触摸外壳时振动明显”,且改变安装方式(如加垫减震垫)后异响减轻。
1. 安装固定的松动与共振
压缩机固定底座的 “螺栓松动”(预紧力从 30N?m 降至 10N?m)会使 “压缩机与底座产生相对运动”,振动幅度增至 0.1mm 以上,发出 “低频的撞击声”(与转速同步)。支架若 “刚性不足”(如厚度从 3mm 减至 2mm)会在振动时产生 “弯曲形变”,引发 “结构共振”,表现为 “持续性的嗡嗡声”,随负载增加(振动加剧)异响增强。
压缩机与底座间的 “减震垫”(如橡胶垫)若因 “老化硬化”(硬度从 50 Shore A 升至 80 Shore A)会使 “减震效果下降”(传递率从 20% 升至 80%),振动直接传递至外壳,发出 “放大的机械噪声”。减震垫若 “安装不对称”(如一侧压缩量 5mm,一侧 1mm)会导致 “压缩机倾斜”,产生 “附加力矩振动”,表现为 “不规则的晃动声”。
解决方法:
- 底座螺栓松动的需 “按规定扭矩重新紧固”(配合防松胶),支架刚性不足的需 “增加加强筋” 或更换厚壁支架(厚度≥3mm),确保固有频率远离压缩机振动频率(差值>20Hz)。
- 减震垫老化的需 “更换同规格减震元件”(硬度 50-60 Shore A),安装时确保 “压缩量均匀”(误差<1mm),必要时增加减震垫数量(如从 4 个增至 6 个),降低振动传递率至 30% 以下。
2. 外部连接管路的振动与撞击
连接压缩机的 “刚性管路” 若 “固定卡子松动”(间距从 30cm 增至 50cm)会使 “管路自由振动长度增加”,在气流脉动下产生 “横向摆动”,发出 “管路撞击声”(与设备外壳或其他部件碰撞)。管路若 “过长且无支撑”(长度>1m)会形成 “悬臂梁结构”,在振动激励下产生 “共振”,表现为 “持续性的低频嗡鸣”。
管路与压缩机接口若 “同心度偏差过大”(>0.1mm)会使 “连接部位受附加力矩”,在振动时产生 “周期性的应力变化”,发出 “细微的咯吱声”(金属变形声)。接口处的 “密封圈过硬”(如氟橡胶硬度 70 Shore A)会使 “振动传递增强”,表现为 “接口附近异响明显”,更换软质密封圈(硬度 40 Shore A)后减轻。
解决方法:
- 管路固定松动的需 “增加固定卡子”(间距≤30cm),确保管路无明显摆动(振幅<0.05mm);过长管路需 “分段支撑” 或 “加装弹性连接管”(如波纹管),减少共振。
- 接口同心度超差的需 “调整管路走向”(用百分表校准,偏差<0.05mm),避免附加应力;更换 “低硬度密封圈”(40-50 Shore A),并在接口处加 “防振垫”(如硅胶垫),降低振动传递。
四、润滑与冷却系统异常:油膜失效引发的 “摩擦异响”
压缩机的机械部件依赖 “润滑油膜”(厚度 0.001-0.01mm)隔离金属接触,若因 “油量不足”(油位低于最低刻度)、“油品劣化”(粘度下降 50%)导致 “油膜破裂”,会引发 “边界摩擦”,产生 “异常摩擦音”,这类异响伴随 “部件温度升高”(比正常高 20℃以上),易与单纯机械磨损混淆。
1. 润滑系统的油量与油质问题
润滑油 “油位低于吸油管口” 会导致 “油泵吸空”,供油压力从 0.2MPa 降至 0.05MPa 以下,轴承与轴颈间 “油膜无法形成”,出现 “干摩擦”,发出 “尖锐的金属摩擦音”,随运行时间延长(10 分钟以上)可能导致部件烧毁。供油管路若 “堵塞”(如滤网杂质过多)会使 “局部供油不足”,表现为 “特定部件(如连杆轴承)的间歇性异响”。
润滑油若 “长期未更换”(超过 2000 小时)会导致 “粘度下降”(40℃运动粘度从 32cSt 降至 15cSt),油膜承载能力不足,在高负荷时(如压力 200kPa)出现 “油膜破裂”,发出 “瞬间的摩擦声”。使用 “错误粘度的油品”(如低温用 22cSt 油在高温环境使用)会因 “粘度不匹配” 导致润滑不良,表现为 “启动时异响明显,运转一段时间(油温升高)后减轻”。
解决方法:
- 油量不足的需 “补充同型号润滑油至规定油位”(油位镜 1/2-2/3 处),供油管路堵塞的需 “清洁滤网和管路”,确保供油压力≥0.15MPa;定期检查油位(每周一次),避免吸空。
- 油品劣化的需 “彻底更换润滑油”(排放旧油后冲洗油路),选用 “推荐粘度的油品”(如 40℃运动粘度 32-46cSt),按运行时间(1500-2000 小时)定期更换,避免高温环境下长期使用(油温≤60℃)。
五、异响的检测与鉴别:科学区分异响类型
准确判断压缩机异响的类型,需结合 “声音特征”“伴随现象”“检测工具”,避免盲目拆解:
- 机械摩擦音:
特征为 “持续的金属摩擦声”,关闭电源后因惯性仍会响 1-2 秒(机械转动惯性),伴随部件温度升高(>环境温度 40℃),可用 “听诊器” 贴紧压缩机壳体,定位摩擦部位(如轴承处声音最明显)。
- 气动噪声:
特征为 “气流啸叫或冲击声”,关闭电源后立即消失,与压力和流量相关(压力升高时异响增强),用 “声级计” 测量,高频成分(1000Hz 以上)占比>50%。
- 振动传递异响:
特征为 “设备整体或管路的共振声”,触摸外壳或管路时振动明显,改变安装方式(如加垫)后异响减轻,用 “振动仪” 测量振幅>0.05mm(正常<0.01mm)。
通过以上方法,可精准定位异响源头,采取针对性措施,将压缩机运行声音恢复至正常范围(声压级<65dB,无明显异常频率成分),避免因异响导致的部件进一步损坏。
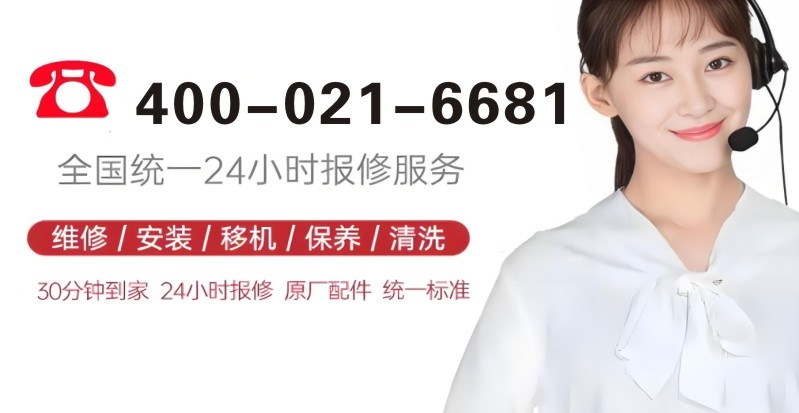